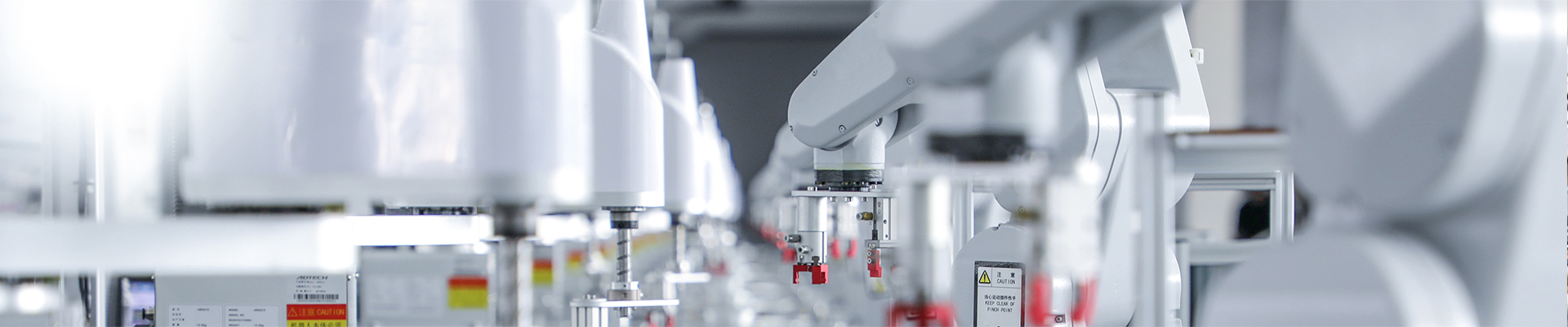
Interpretation of Hydrodynamic Coupling Model Codes
2025-05-19 08:39Interpretation of Fluid coupling Model Codes
The model codes of Fluid couplings encapsulate critical technical specifications and functional characteristics, serving as a key reference for equipment selection. This analysis systematically deciphers the coding logic across different manufacturers and application scenarios.
I. Standardized coding structure for Fluid coupling
Fluid coupling models generally follow a "letter + number + letter" structure, with each segment conveying specific technical information:
1.Prefix Letters (Core Function Identification)
Y: Denotes hydraulic transmission systems (from Chinese "Yèlì")
O: Indicates coupling type (from Chinese "Ōuhéqì")
X: Represents torque-limiting characteristics (e.g., YOX450)
Variations:
YOT: Speed-regulating type
YOS: Dual-chamber design
Example: In the YOXD series, "D" signifies water-based media compatibility for mining applications.
2.Fluid coupling value section (Core Parameter Specification)
The numeric value (e.g., 450 in YOX450) typically corresponds to the nominal diameter (in mm) of the working chamber.
Diameter ranges from 200–800 mm, accommodating power transmission from 15 kW to 4,000 kW.
Torque transmission capacity increases proportionally with the fifth power of the diameter and the square of rotational speed.
3.Suffix Letters (Extended Function Codes)
IIZ: Integrated brake wheel for rapid stopping in conveyor systems
A: Pin-type coupling for 0.3°–0.5° axial misalignment compensation
V: Extended auxiliary chamber for 20%–30% enhanced heat dissipation
SJ/D: Water-medium models for explosive environments (e.g., coal mines)
R: V-belt pulley integration for non-direct drive systems
II. Technical and Economic Implications of Model Variations for Fluid coupling
1.Material Cost Differences
Aluminum alloy housings (YOX) cost 40% less than steel counterparts (YOS).
Imported bearing configurations increase prices by 25%–35%.
2.Performance Gradients
Speed-regulating models (YOT) cost 3–5× more than torque-limiting equivalents.
Brake-equipped IIZ models command 15%–20% price premiums.
3.Customization Costs
MA certification is mandatory for mining equipment in China.
Marine models require CCS certification codes.
IV. Selection Methodology for Fluid coupling
1.Operational Matching Principles
Select torque-limiting models (X-type) with overload coefficients ≥2.2 for impact loads.
Prioritize ≥96% efficiency speed-regulating types (YOT) for continuous operations.
Mandate IP55-rated water-medium models (SJ/D) for dusty environments.
2.Key Parameter Guidelines
Power matching requires aligning motor output with load demands using standardized formulas.
Verify overload protection coefficients (≥1.5) for shock loads.
3.Lifecycle Cost Considerations
Compare 10-year energy consumption: Base models consume 8.2M kWh annually vs. 7.8M kWh for IIZ types.
Maintenance frequency drops from 2 to 1 service events/year for premium models.
V. Application-Specific Recommendations for Fluid coupling
1.Conveyor Systems
Use YOXIIZ series with integrated brakes for controlled stopping.
Implement V-type cooling for >200 kW drives.
2.Ball Mill Drives
Mandate torque limiters with ≥2.5 overload coefficients.
Opt for water-medium models (D-type) with temperature monitoring.
3.Marine Propulsion
Dual-chamber YOXS series ensures redundancy.
Specify anti-corrosion coatings for saltwater exposure.
VI. Technological Evolution for Fluid coupling
1.Smart Integration
IoT-enabled couplings (marked S) now offer real-time performance monitoring.
2.Material Advancements
Carbon fiber housings reduce weight and cost by 30%.
Nanofluid media boost efficiency by 2%–3%.
3.Standardization Trends
ISO 17804:2024 unifies global naming conventions.
China’s GB/T 5837-2025 introduces eco-certification labels.
Conclusion
Decoding Fluid coupling models requires understanding regional coding practices, functional suffixes, and application-specific requirements. For critical installations, always request manufacturer test reports and third-party validation. When selecting models, prioritize compatibility with operational demands, verify certification marks, and evaluate total lifecycle costs.