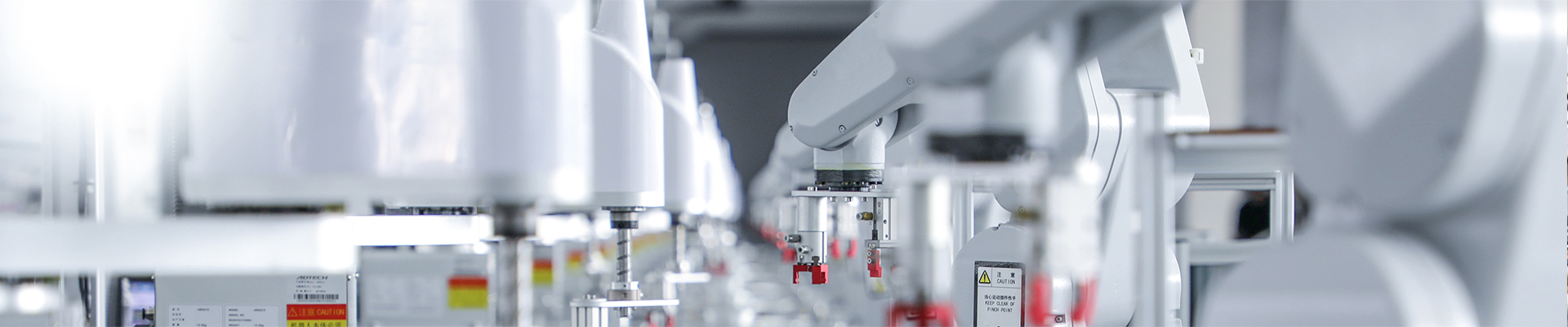
Objective technical introduction to coupling and their application scenarios
2025-07-15 07:50I. Definition and Core Functions of Couplings
A coupling is a mechanical device that transmits power via a medium, connecting prime movers (e.g., motors) and driven machines (e.g., pumps, fans) for non-rigid power transmission. Core functions include:
Vibration Damping: Absorbs shock loads during startup/operation and isolates torsional vibrations to protect equipment .
Light-Load Starting: Reduces motor startup load, shortens startup time, and minimizes grid impact .
Overload Protection: Automatically disconnects power transmission when load exceeds limits, preventing damage to motors and machinery .
Multi-Motor Coordination: Balances load distribution in multi-motor drives to ensure synchronous operation .
II. Classification and Working Principles
1. Hydrodynamic Coupling
Structure: Consists of a pump wheel, turbine wheel, rotating shell, and working fluid (typically oil) .
Principle: The pump wheel converts mechanical energy into fluid kinetic energy; the turbine wheel reconverts it into mechanical output, enabling contactless power transmission .
Features:
Suitable for high-power, high-inertia loads;
Wide speed adjustment range (e.g., feedwater pumps in power plants) .
2. Mechanical Flexible Coupling
Types: Include spring couplings (e.g., serpentine spring couplings) and rubber block couplings .
Principle: Compensates for axial/radial misalignment via elastic elements (springs, rubber) while transmitting torque .
Features:
Compact structure and low maintenance;
Ideal for precision transmission (e.g., CNC machine tools) .
III. Key Application Scenarios
1. Energy & Power Industry
Power Plant Feedwater Pumps: Hydrodynamic couplings adjust pump speed, replacing high-pressure valves to simplify systems and reduce failures .
Wind Turbines: Flexible couplings mitigate vibrations in turbine main shafts caused by aerodynamic loads .
2. Heavy Industry & Mining Machinery
Mining Equipment: Hydrodynamic couplings enable heavy-duty startups and overload protection for belt conveyors and crushers .
Metallurgical Equipment: Balances load distribution in multi-motor drives for rolling mills .
3. Transportation & Marine
Automotive Transmissions: Hydrodynamic couplings ensure smooth starts and power interruption protection in automatic gearboxes .
Ship Propulsion: Flexible couplings reduce impact vibrations between engines and propellers .
4. Precision Manufacturing & Automation
CNC Machine Tools: Mechanical flexible couplings limit transmission errors to <±5 arcseconds .
Industrial Robots: High-precision couplings compensate for joint assembly deviations, enhancing motion stability .
IV. Technical Comparison & Selection Reference
Type
Applications
Advantages
Limitations
Hydrodynamic Coupling
High-power, high-inertia loads (>100kW)
Strong overload protection, speed control
Large size, fluid maintenance required
Mechanical Flexible Coupling
Medium-low power, precision transmission
Simple structure, maintenance-free, high misalignment tolerance
Limited torque capacity
V. Industry Trends
Intelligentization: Integrated sensors monitor temperature/vibration for predictive maintenance .
Lightweighting: Composite materials (e.g., carbon fiber-reinforced elastomers) reduce rotational inertia .
Cross-Industry Expansion: Growing demand in emerging fields like nuclear reactor coolant pumps and hydrogen compressors .
Sources:
Hydrodynamic Coupling Technical Specifications
Industrial Coupling Application Whitepaper
Power Plant Feedwater System Design Standards
Mechanical Transmission Component Selection Guide